The decorating is all but done, awaiting some glass for the dining room doors, but have done some prep and even thinking about how to do this project.
I have limited facilliites, but fond memories of machining at school in metalwork and my early years of my apprenticeship back when I was 16, which was a very long time ago.
Thus, preparation was needed to get ready for the machining, build, and hopefully running of this 'big' diesel, big at least in model aero plane terms though I only fly electric.
My lathe is a fabulous 1922 or so Drummond round bed lathe which eventually was given to Myford just at the end of the WW2 era. The history of the lathe design is as facinating to me as doing anything on it.
It has been a god-send when building the Lola hillclimb car and various old motorcycles etc over the years.

x 10
It came via ebay and a sale from the very back of a village garage deep in the Lake District when i retired from boring work. I built a floor stand for it and it has been great, will skim a thou or two easy esp since fitting it with a new Chinese 3 jaw chuck, and recently a 4 jaw.
The Myford cross slide pictured above makes this lathe into a versatile milling machine for this scale of work and was cheap and is new.
To make the parts to this engine I need to expand the lathe's capabilities to cut threads. That sounds easy which is is on a more modern higher-end lathe than this Drummond which would have been treadle powered(!)
The steel cylinder and the aluminium crankcase are screwed together firmly using a 24 tpi thread on around 3/4" diameters, yes, this engine is all in Imperial and the Drummond has NO indexing on any movement, so you machine and iterate to the size.
Digital calipers are my best friend.
To get threads cut you need to gear the head stock spindle to give 1 thread in a 24th of an inch.
Thus you have a chain of spur cut gears that come off the headstock spindle to the lead screw that dog clutches together to give this movement/turn.
The lathe came with a number of gears from 15 Teeth to 125 teeth, but the main cluster counts up in 5's, ie 30 teeth, 35 teeth etc.
By swapping the gears around you can get many TPI threads, and after considerable swapping about this was achieved, took 2 hours in all...This Drummond was sold as a budget lathe capable of thread cutting back in the day.
Those familiar with powered machines will appreciate the fright of the risk that the tool crashes into the chuck/work piece and the damage that can ensue, and thread cutting is one of those risky things, so the trick is to drive the spindle very slowly, ie 20 turns/minute of less. This way you can stop the lathe and risk of the crash.
So, the first mod to the lathe is to allow the spindle to be turned by hand, that is add a hand crank to the spindle substituting the electiric drive motor totally.
Oddly, this was dead easy(!) and a plug socket welded to the 1922 gear clamp nut allowed me to put a good double ended ring spanner on the socket end and add a wood handle for comfort when turning the spindle.
I made a 'bolt' to engage the gear train to the dog clutch to the lead screw, and with the gear set got 24 tpi for a cross slide/ tool post movement of 1 inch.
Hope you are keeping up at the back!
Next came a test, so with a simple pointed tool bit and some steel about 5/8" dia I first covered the steel bar protruding out of the chuck (about 1.25") with marking blue.
I added a 'cut' on the cross slide and wound the spindle. This grazed the surface like a scriber would and a nice clean helix was 'cut' into the steel surface.
Wound the spindle back and the tool free of the steel bar. The leadscrew remember is still all engaged together (important fact), NEVER disengage the lead screw.
Added a real cut, about 10 thou, and wound on again to cut a start to the thread which exactly followed that scribed helix previously, which started the thread cut form, it actually worked!
Further back and forth and I had a nice thread on the bar, my first self cut male thread since i was 16 on a lathe. (actually a square acme thread on a simple screw jack, still have it).
Harold, my tutor as an apprentice would be proud!!
With this, I bought a set of internal and external thread cutting tips and also some old school 3/16" HSS for the old tool holders I have, so now fully set up with tools, and getting closer to 'All the gear, and no Idea' elevation.
Time now to study the design and the drawings and decide which part to make first that is the simplest.
Enough boring words, a few pics taken along the line to amuse.
Anyone notice the head-scratching I had with the last picture?
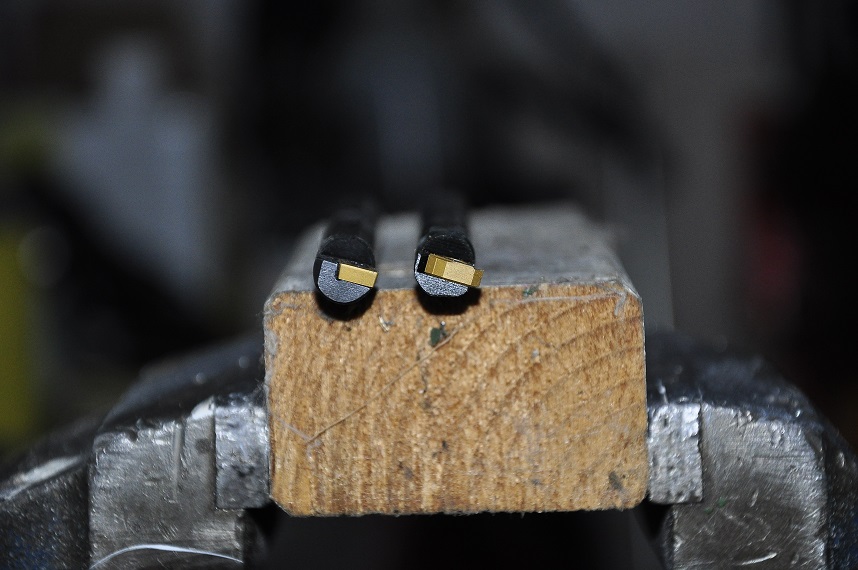